08. março 2023
, Notícias
Combining sustainability and cost reduction
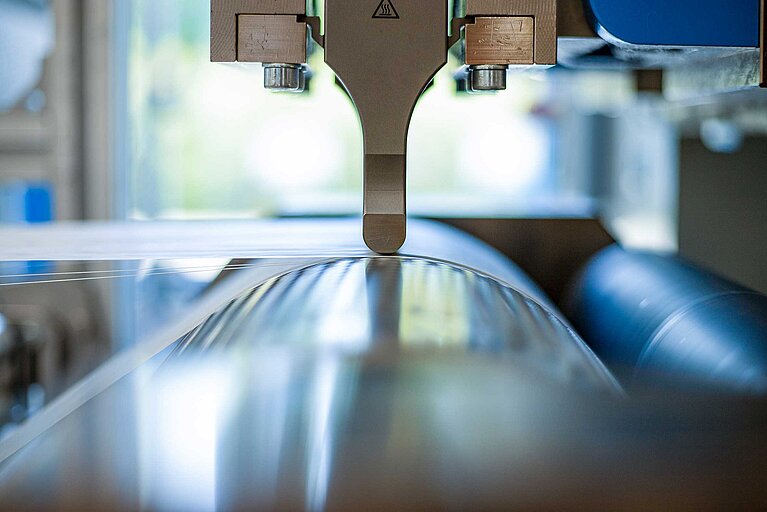
To make the costly process of elastic fixation in nonwovens more efficient, Herrmann Ultraschall has developed an innovative process: the anchoring of elastic threads with ultrasonics. Producers benefit from a flexible, stable and sustainable process that improves the customer experience while reducing production costs.
This patented anchoring process is based on a new type of sonotrode. Thanks to its unique surface structure, the welding tool creates a tunnel between the nonwoven layers, through which the elastic threads are guided. Depending on the application, specific welding points are created continuously or intermittently, in which the threads are anchored in the nonwoven only by means of ultrasonics.
Thanks to the ultrasonics, a distinct advantage is that the anchoring of elastic threads does not require any additional joining agents. Compared to conventional bonding processes, this significantly reduces resource and energy consumption and thus overall manufacturing costs. The elimination of chemicals also improves the feel, the sustainability balance of the products and their durability, as the elasticity of the threads is retained for a longer period of time.
At the same time, the ultrasonic process significantly reduces the risk of thread breakage because the elastic threads do not come into contact with the welding tool during the anchoring process. Instead, they are slightly deformed by the special shape of the tunnels created by the sonotrode, so that after anchoring, the surface friction between the filaments and the nonwovens increases, thus improving their adhesion.
Compared to previous solutions that relied on ultrasonics, thread guidance via the sonotrode also offers additional benefits: "Previously, you needed an anvil roller that was specially engraved for an application. This made precise thread guidance costly and complex," explains Dr. Raquel Roussel-Garcia, Application Development NONWOVENS at Herrmann. "Thanks to the innovative geometry of the guiding channels in the sonotrode, we can implement many different material combinations and product sizes with a single tool. This minimizes investment costs and makes the process much more flexible." Since the sonotrode is part of a simple quick-change system, it is also possible to reduce downtime and maintenance costs in production, she added.