Difficult welding for medical secretion canister
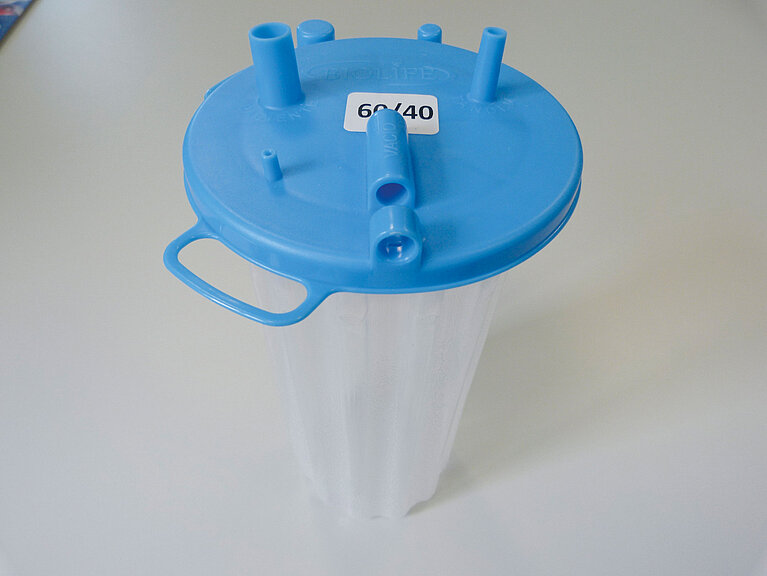
Precise force control for soft plastics
A material that is difficult to weld, large component dimensions, and the required strength/sealing specifications – the ultrasonic laboratory at Herrmann Ultraschall was able to solve this challenging task for a manufacturer of medical technology.
Polyethylene (PE) is a very soft plastic that strongly dampens ultrasonic waves and therefore requires high welding amplitudes greater than 40 μm to melt the material. Since ultrasonic generators have become available that deliver high and reliable power over a long period of time, it is possible to solve such welding applications with ultrasonics.
The component size also plays an important role, because the larger and more complex the dimensions, the more difficult it is to correctly introduce the ultrasonic waves into the joining zone.
The application described involves septic tanks made of PE such as those used in hospitals to collect bodily fluids. The challenge was to weld a lid made of high-density polyethylene (PE-HD) to a body consisting of a mixture of PE-HD and PE-LD. Difficult requests like this are often solved using hot plate welding. However, this technology does not provide enough quality-relevant process data to meet the demanding production requirements of industries such as medical technology. Ultrasonic welding, on the other hand, was able to successfully complete the project and meet all customer and market requirements for medical technology parts.
The customer specified the following requirements:
- Lid and body have to be welded together with a strong bond, as the container is used in the hospital to collect bodily fluids. Therefore, the container must withstand drop heights of 1.5m and pressure surges of up to 0.8 bar.
- The circumferential weld joint requires a sonotrode design that converts the high amplitude uniformly.
- The welding result has to be free of imprints and requires careful finishing of the welding tool.
- A height adjustable fixture accounts for the different heights of the line of products.
- Process validation and traceability
Weld force profiling and a graphic display of the parameters
One advantage of ultrasonic welding is the rich parameterization and its visual display. The ultrasonic welding machine, HiQ DIALOG 6200, used for this project offers weld force profiling up to three welding forces and a 15" display. The ability to change the weld force during the process supports the welding of demanding materials and geometries.
The progress of the welding process can also be shown on the display. The visualization on the user interface of the control system shows deviations and enables the optimization of the welding process. The course of the joining speed curve (weld depth over time) is a decisive indicator here. With the evaluation of the parameter graphs;
- Weld Depth
- Amplitude
- Frequency
- Power
- Force
, the laboratory team at Herrmann succeeded in the difficult process setting.
A powerful generator
The fully digital ultrasonic generator delivers 6200 watts of power and records more than twenty readings 10,000 times per second. This allows the welding process to be controlled faster and more sensitively which makes the entire welding process more reproducible. The output amplitude can be programmed continuously from 1-100% and can be precisely matched to the plastic material even with a high damping coefficient. The control electronics with a sampling rate in the megahertz range (1μs) ensures precise amplitude constancy under all operating conditions, as in the present case of the circumferential weld joint and the high amplitude required due to the material.
Tracking software for traceability
One of the important requirements in medical technology is process safety and traceability. Herrmann Ultraschall supplies an integrated FSC software module that records changes to system parameters and user actions in electronic audit trails. In combination with the DataRecorder software module, which allows the permanent storage of process results on a PC directly from the ultrasonic generator, both welds and user actions such as parameter changes can be recorded completely in the interests of a holistic production logbook.