Erfolgsgeschichte KACO
Für die Versiegelung einer Membran in einem Notentgasungssystem suchte KACO nach einem präzisen und schnellen Fügeverfahren. Dank der engen Zusammenarbeit konnte Herrmann Ultraschall nicht nur den idealen Schweißprozess für diese Vorgaben entwickeln, sondern auch weitere Anwendungsgebiete der Ultraschall-Technologie aufzeigen und damit die Produktion des Systems noch effizienter gestalten.
Die Herausforderung
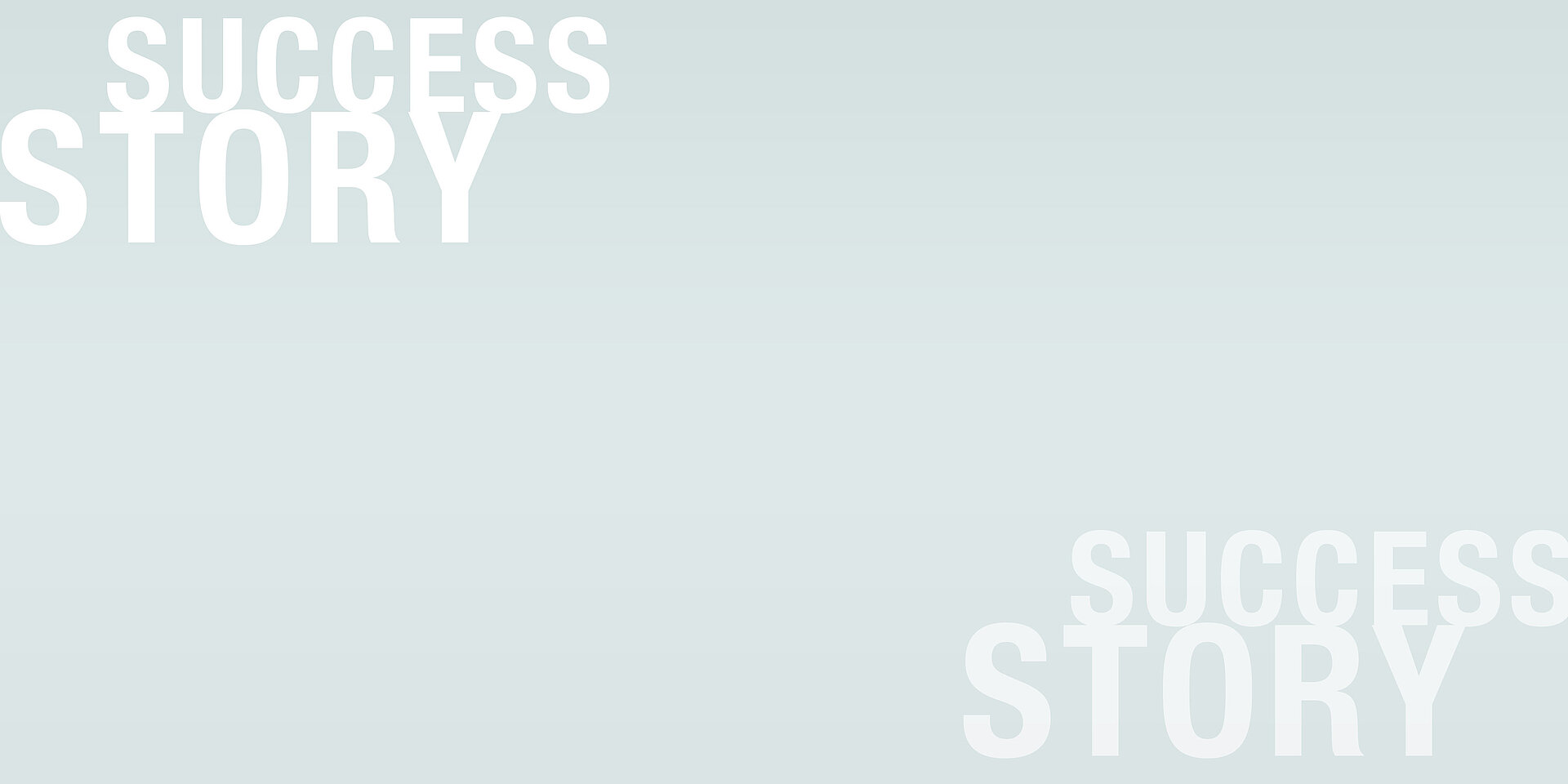
Trotz ihres geringen Gewichts und einer leichten Wölbung muss die Membran exakt mittig in das Gehäuse eingepasst werden. Da alle Bauteile der Anwendung genau aufeinander abgestimmt sind, kann es bei einer unsauberen Platzierung der Membran zu Beeinträchtigungen der Funktionsfähigkeit innerhalb des Systems kommen.
Alternative Fügeverfahren, wie etwa das Kleben, schieden aus. Es zeigte sich, dass mit diesem Verfahren eine exakte Zentrierung der Membranen aufgrund der Verformung nur schwer umsetzbar gewesen wäre. Zudem hätte das Aushärten des Klebstoffs zu längeren Produktionszeiten geführt und die Chemikalien hätten sich negativ auf die Atmungsfähigkeit der feinen Membran auswirken können.
Individuell, pneumatisch, sicher
Um die exakte Zentrierung des Fügepartners in der Applikation sicherzustellen, entwickelte man eine individuelle Haltevorrichtung, die in die Werkstückaufnahme integriert wurde. Sie erleichtert es dem Benutzer am Handarbeitsplatz, die Membran ideal für den Schweißprozess zu positionieren und verhindert ein Verrutschen des Fügepartners.
Für die Schweißversuche wurde diese Haltevorrichtung noch manuell bedient, in der Serienproduktion soll sie automatisiert über Pneumatik gesteuert werden.
Durch die Kombination einer solchen individuellen Haltevorrichtung sowie einer Anpassung der Schweißparameter konnte die exakte Versiegelung der Membran gewährleistet werden.
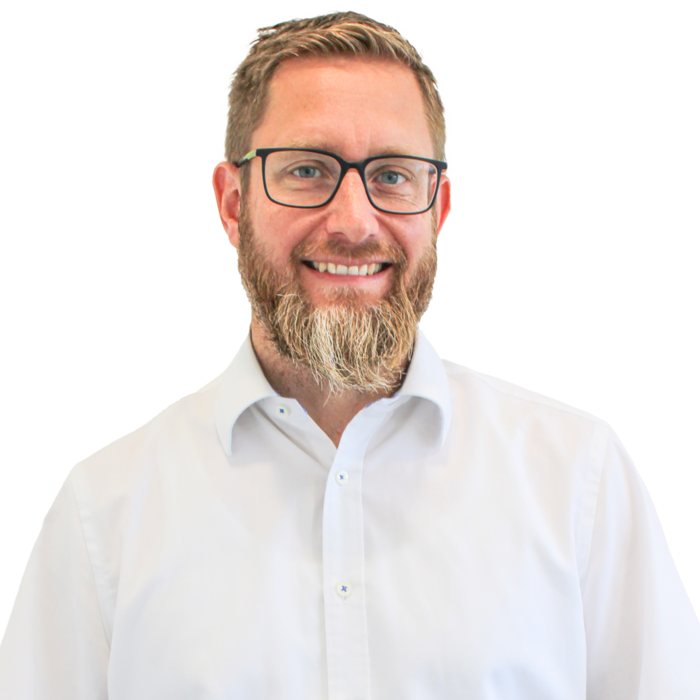
„Für das Unternehmen KACO ist die Batterieentlüftung ein neues Produkt mit vielen Herausforderungen in der Bauteilauslegung und den dazu notwendigen neuen Fertigungsprozessen.
Daher haben wir uns sehr darüber gefreut mit Herrmann Ultraschall einen Partner gefunden zu haben, der uns bei der Auslegung der notwendigen Schweißkonturen und des Ultraschallschweißprozesses vom Projektstart über diverse Laborbesuche bis zur Serienfertigung immer kompetent begleitet hat."
Simon Kayser, Manager Advanced Engineering Processtechnology / Product KACO
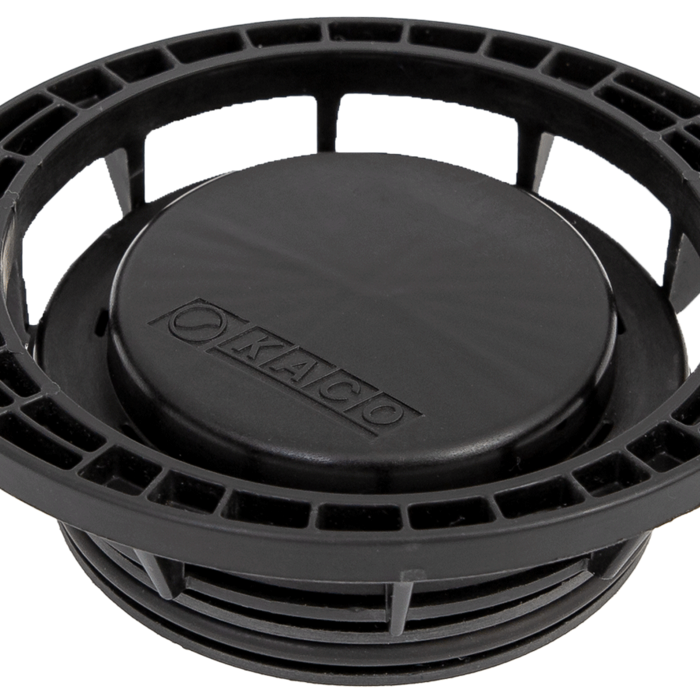
Schweißung des Kunststoff-Deckels
Gemeinsam wurden weitere Schweißprozesse entwickelt, um etwa den Kunststoff-Deckel für das Notentgasungssystem auf das Kunststoffgehäuse mit der versiegelten Membran zu verschweißen. Dabei legte KACO größten Wert auf eine stoffschlüssige Verbindung der beiden Fügepartner. Diese Anforderung konnte bereits in den ersten Schweißversuchen im Labor umgesetzt werden.
Einsenken der Messingbuchsen
Um die Sicherheit der Batterie zu gewährleisten, werden jeweils vier solcher neuentwickelten Notentgasungssysteme pro Batteriekasten befestigt. Für diesen Zweck werden pro System zwei Messingbuchsen in das Kunststoffgehäuse der Applikation eingelassen. Da dieser Prozess ebenfalls mit Ultraschall realisiert werden kann, entschied sich KACO nach einer Beratung mit dem Herrmann-Team dazu, auch hier auf das zuverlässige Fügeverfahren zu setzen. Das Einsenken von Messingbuchsen mit Ultraschall schont das Material und sorgt gleichzeitig für ein Ergebnis mit perfekter Optik.
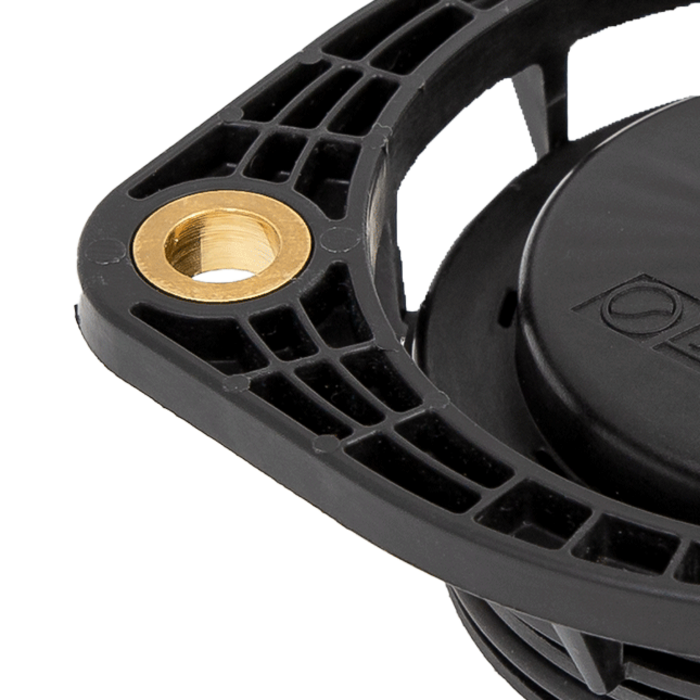
Enge Beratung eröffnet volles Ultraschall-Potenzial
Das gemeinsame Schweißprojekt zwischen KACO und Herrmann verdeutlicht die Vielseitigkeit der Ultraschall-Schweißtechnologie. Von der Versiegelung der Membran über die Verschweißung zweier Kunststoffbauteile bis hin zum Einsenken von Messingbuchsen in das Gehäuse bietet das Fügeverfahren bei jedem Prozessschritt mit präzisen, sauberen und schnellen Verbindungen einen enormen Mehrwert.
Entscheidend dafür ist ein erfahrener Ultraschall-Experte, der durch eine enge Zusammenarbeit mit dem Kunden dessen Bedürfnisse erkennt und beim Einsatz der Fügetechnologie beraten kann. Das ermöglicht es, das volle Potenzial des Ultraschallschweißens für eine wirtschaftliche und effiziente Serienproduktion zu nutzen.