Batterien ermöglichen eine emissionslose und nachhaltige Mobilität. Aber es wird Zeit, dass auch die Herstellung der Batterien nachhaltig wird. Deshalb haben wir mit CUSTOMCELLS®, einem der weltweit führenden Entwickler kundenspezifischer Lithium-Ionen-Batteriezellen, nach neuen Wegen gesucht, die Batterieproduktion von Grund auf zu optimieren – und die Lösung gefunden.
Mit modernen Ultraschall-Schweißmaschinen und dem Know-how aus mehreren Jahrzehnten Ultraschall verbessern wir maßgeblich die Sicherheit, Effizienz und Energiebilanz der Produktion.
"Mit Herrmann Ultraschall haben wir einen zuverlässigen Partner im Bereich der sicheren Schweißverbindungen an unserer Seite. Die Ultraschallgeräte von Herrmann tragen maßgeblich zur Verbesserung unserer Produktqualität bei. Bei Customcells legen wir großen Wert auf Nachhaltigkeit und Energieeffizienz und sind daher äußerst zufrieden mit der hervorragenden Zusammenarbeit und der gemeinsamen Umsetzung neuester Technologien. Wir können Herrmann Ultraschall uneingeschränkt weiterempfehlen."
Christian Zender, Director Customcells Tübingen GmbH
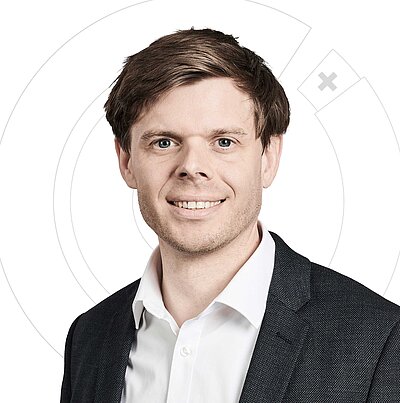
Die Herausforderung
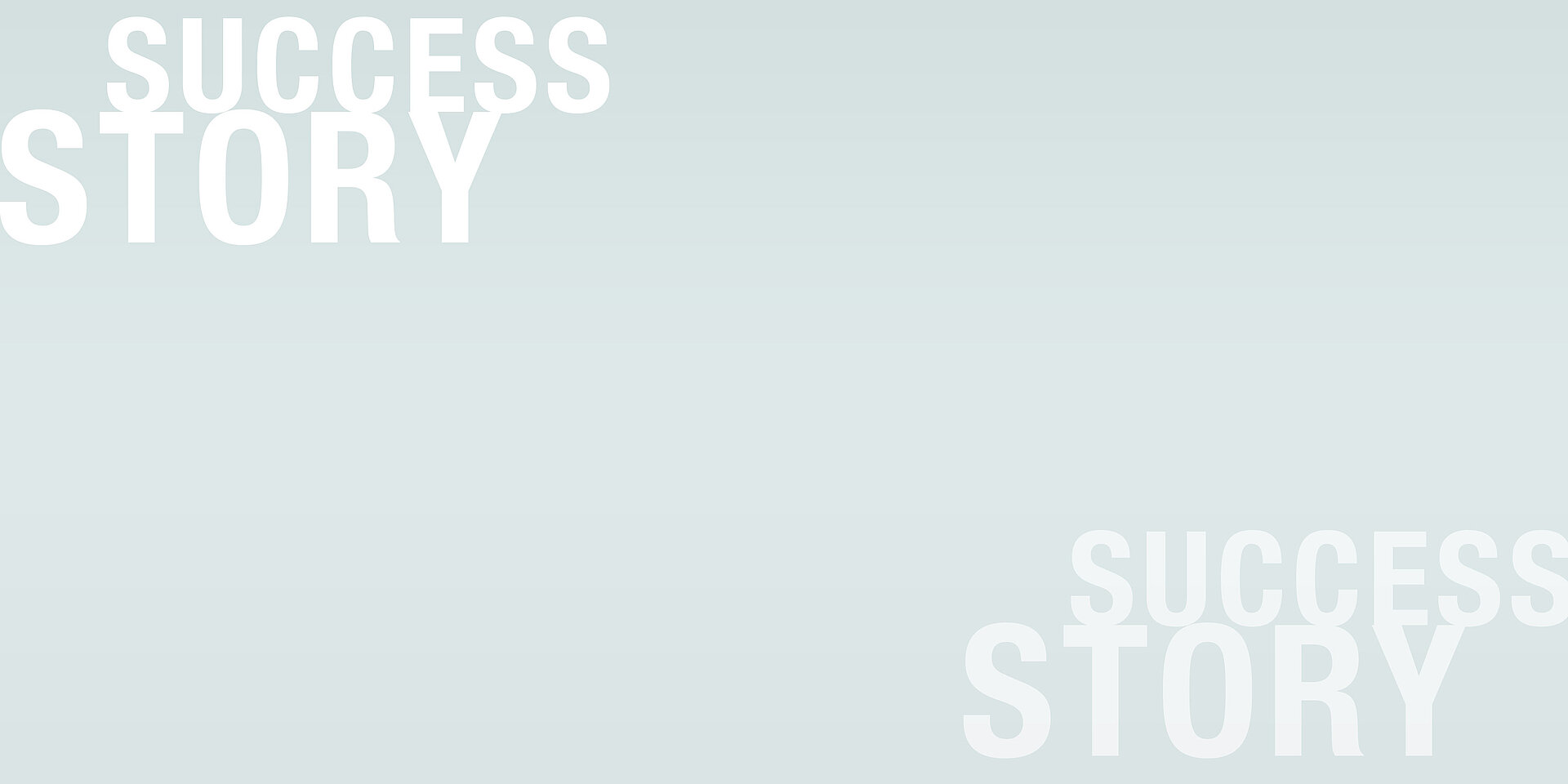
Fügeverfahren wie das Ultraschallschweißen kommen in der Regel am Ende der Batterieproduktion zum Einsatz. Das heißt, dass bei fehlerhaften Prozessen die gesamte Batteriezelle entsorgt werden muss. Das führt zu hohen Kosten in der Produktion, die vermieden werden können. Dennoch werden bislang Ausschussraten von bis zu 20 Prozent in der Branche akzeptiert.
Der Anspruch von Herrmann Ultraschall und CUSTOMCELLS® besteht darin, einen sicheren Schweißprozess zu entwickeln, der dem nachhaltigen Anspruch der Batterie-Branche gerecht wird. Dafür braucht es ein schonendes, präzise steuerbares Verfahren, um die sensiblen Materialien der Batteriezellen nicht zu beschädigen.
Energieeffizientes Verfahren benötigt
Der Status quo in der Batterieproduktion von Pouch-Zellen ist alles andere als nachhaltig: Die sensiblen Materialien werden häufig noch mit thermischen Fügeverfahren wie dem Heißsiegeln verbunden. Der Energieverbrauch ist hoch – ebenso wie das Risiko, die Materialien dabei zu beschädigen. Dabei gibt es eine sicherere und umweltfreundlichere Alternative, die bereits in einer anderen Branche für hohes Einsparpotenzial sorgt.
Ultraschall senkt Energieverbrauch
Pouch-Verpackungen werden seit Jahrzehnten mit Ultraschall versiegelt mit enormen Vorteilen für Unternehmen: Das effiziente Verfahren spart bis zu 75 Prozent Energie ein. Denn Ultraschall funktioniert ohne externe Wärmezufuhr, Hitze entsteht nur für während der kurzen Schweißzeit von 100 bis 200 Millisekunden im Inneren der Materialien durch Reibung. Die Schweißwerkzeuge selbst bleiben kalt und sind unmittelbar einsatzbereit – ein Aufheizen entfällt und spart somit weiter Energie
Dieses Know-how aus tausenden gelösten Anwendungen konnte Herrmann erfolgreich auf das Schweißen von Pouch-Zellen übertragen.
Prozessdaten geben Sicherheit
Im Schweißen von Kunststoffen erreichen Ultraschall-Schweißsysteme von Herrmann Ausschussraten nahe den 0 Prozent. Der Schlüssel liegt in der Prozessüberwachung: Bei jeder einzelnen Schweißung werden bis zu 150 Parameter erfasst und gespeichert. Die wichtigsten davon können in Echtzeit grafisch dargestellt werden. Das sorgt für ein reproduzierbares Schweißergebnis und minimiert den Ausschuss.
Dieselbe Menge an Daten entsteht auch jedem einzelnen Ultraschall-Schweißvorgang von Batteriezellen. Werden Sie richtig genutzt, können sie den Schweißprozess von Batteriezellen nachhaltig optimieren. Damit gelingt es, die Ausschussrate um ein Vielfaches zu reduzieren und damit auch die Kosten und den Materialverbrauch.
Der Praxistest
Gemeinsam mit CUSTOMCELLS® hat Herrmann die Erfahrungswerte aus über 60 Jahren Ultraschall in die Praxis übertragen. Dabei werden die Maschinen des Ultraschall-Spezialisten für die Vor- und Hauptschweißung an Pouch-Zellen eingesetzt. Die Besonderheit: Die von CUSTOMCELLS® entwickelten Batteriezelle nutzen Tabs, die in diesem Schweißprojekt deutlich kleiner als branchenüblich ausfallen.
Um eine zuverlässige, stoffschlüssige Verbindung zwischen Tab und Anode beziehungsweise Kathode sicherzustellen, wurden die Sonotroden der Ultraschall-Schweißmaschinen präzise auf die jeweilige Größe der Tabs angepasst.
Ergebnisse aus dem Labor bestätigt
Schweißversuche im Ultraschall-Labor ergaben, dass die von CUSTOMCELLS® genutzten Zellen sicher und schonend mit einem bereits entwickelten, speziellen Sonotrodendesign verbunden werden können.
Nach kurzer Zeit konnten auch die dazu passenden Schweißparameter definiert werden. Damit erfolgte die Umstellung auf die Herrmann-Schweißsysteme nahezu ohne Stillstandszeit für die Produktion. Unter den dortigen Produktionsbedingungen zeigte sich: Die Maschinen liefern auch in der Praxis einen sicheren, energiesparenden Fügeprozess für die Batteriezellen.
Gemeinsame Entwicklungsarbeit liefert optimalen Schweißprozess
Ultraschall ist die richtige Technologie für eine schonende, starke und gleichermaßen umweltfreundliche Verbindung von Pouch-Zellen. Das hat die Zusammenarbeit mit CUSTOMCELLS® gezeigt, in der die Vorteile der Fügetechnologie in der Praxis unter Beweis gestellt werden konnten. Dabei hat sich gezeigt, wie wertvoll die langjährige Erfahrung in der Nutzung mit Ultraschall auch aus anderen Branchen für die Herstellung von Batterien ist. Diese kann durch die Nutzung von Ultraschall sicherer, umweltfreundlicher und effizienter gestaltet werden.
Neben der Erfahrung ist eine kompetente Beratung und ein flexibler Service durch den Ultraschall-Partner entscheidend, um im Bedarfsfall umgehend auf Veränderungen im Produktionsprozess reagieren zu können. Das Zusammenspiel aus passenden Schweißlösungen und gutem Service bildet die Grundlage für eine reibungslose Produktion von Batterieapplikationen mit Ultraschall.