15. July 2025
, News
Ultrasonic welding of copper and aluminum
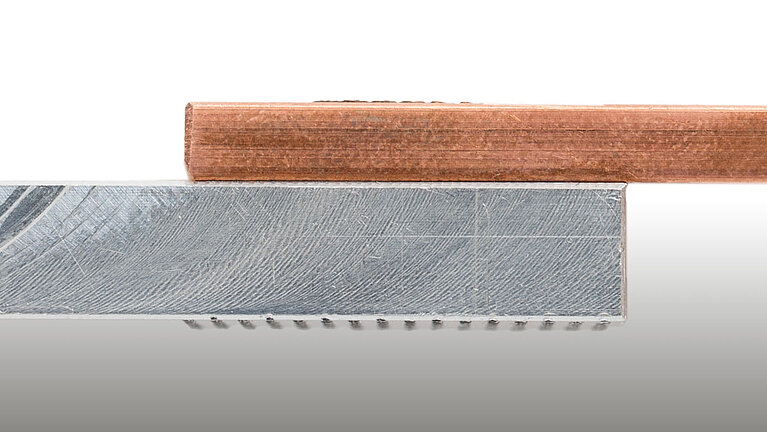
In modern busbar manufacturing, for example for battery modules, power electronics or power distribution systems, the connection of copper and aluminum has long been standard. However, the implementation is technically demanding and in many manufacturing processes leads to rejects and unreliable connections that lose quality over time.
The reason: many conventional joining processes reach their limits with such mixed joints. Differences in material properties lead to quality problems, unstable connections or complex manufacturing processes.
Ultrasonic welding offers a particularly process-stable, material-friendly and economical alternative that has proven itself in numerous industrial applications.
Copper and aluminum differ significantly both in their physical properties and in their behaviour during joining:
These differences often lead to problems with thermal processes such as laser welding, soldering or resistance welding:
Ultrasonic welding does not use heat to join metals such as copper and aluminum, but rather high-frequency mechanical vibration and pressure. This combination makes it possible to join metals in a solid condition and avoid the typical weaknesses of other processes.
As the material is not melted, no brittle intermetallic connections can form. The connection is made directly by plastic deformation of the contact surfaces: solid, homogeneous and reliable.
With aluminum in particular, the oxide layer is a major obstacle to electrical and mechanical connections. The ultrasonic vibration ensures that this shift is broken down directly in the process end. This creates a clean, metallic contact surface - without any chemical pre-treatment.
As no strategic heat is applied, it doesn't matter whether copper absorbs more heat or aluminum deforms faster. The process is robust against material differences - and therefore particularly suitable for the connection of non-ferrous metals such as copper-aluminium, aluminium-brass or other bimetal connections.
Mixed joints such as copper and aluminum can only be produced with limited reliability using conventional methods. Ultrasonic welding offers a clear advantage here: it connects differences in metals without melt, without additives - and with high electrical and mechanical quality.
✅ High strength - even in tray and shear direction
✅ Very low contact resistance - <0.1 mΩ possible
✅ No solder required
✅ Short cycle times of 7-12 seconds and high automation capability
✅ Perfectly suitable for Cu-Al and other bimetal connections
Learn more about ultrasonic welding of busbar applications: