Ultrasonic Metal welding
Metal welding is used in the automotive and electronics industries to produce batteries, cable connections, etc. In metal welding, metals are welded in high temperatures, for instance. We differentiate between metal active gas (MAG) and metal inert gas (MIG) welding. Active gases form a connection with the metal, inert gases do not.
Ultrasonic welding, on the other hand, uses ultrasonic waves to join the metals. The ultrasonic welding of metals is a cold welding process, as barely any heat is generated apart from at the weld spot. At this point, high-frequency sound waves are introduced to the parts being welded. Precise tools make it possible to retain a consistent quality during each weld process, and to have reproducible results each time.
Advantages of ultrasonic metal welding
The ultrasonic metal welding process has a few advantages compared to conventional welding methods such as gas metal arc welding:
- Ultra fast: The entire process lasts for mere split seconds.
- Precise: Ultrasonic welding is spot-on. A vast number of welding parameters ensure precise and reproducible results. This is particularly important for welding the smallest metal parts, e.g. in batteries.
- Cost-efficient: No other additives such as solder are required.
- Environmentally friendly: Very little energy is consumed and no chemicals are used.
- Characteristic: Ultrasonic welding ensures a high degree of strength and excellent electrical conductivity at the joined points.
- Gentle: The metals are not damaged or deformed apart from the weld spot.
- Safe: No sparks or smoke are generated during ultrasonic welding.
How ultrasonic welding of metal works
The generator provides a high frequency. This frequency is then transformed into mechanical vibrations in the converter. The amplitude transformer changes the amplitude of the vibrations. The sonotrode can do this as well. Its main task is to introduce the ultrasonic energy into the top of the application horizontally. The ultrasonics cause it to move while the anvil holds the bottom of the application in place. Friction is generated. Here, the roughness peaks of the metal are rubbed off, the top (oxide) layer is broken up and the metal is plastically deformed. Now, the applications can be joined without them melting. This is perfect for welding thin metal, films and wires.
The ultrasonic metal welding process essentially causes materials to become so plasticized that the molecules of both layers end up mixing together. This type of vibration welding causes materials to move so fast that the different layers become intermixed. When the tool is taken away, what results is a single solid piece, as opposed to two separate ones, thanks to the molecules being forced into forming new bonds with each other. In addition, the amount of power required for creating this type of cold metal welding bond is much less than a traditional welding system, while also leaving a stronger weld. For these reasons and many more, ultrasonic welding can be the ideal solution for many kinds of bonding applications.
Areas of application for ultrasonic welding of non-ferrous metals
Ultrasonic welding is used in various industries and sectors:
Battery: There is an increasing demand for lithium-ion batteries (LIBs). Joining anodes (copper foil) and cathodes (aluminum) together requires the best joining technology with long-term process reliability. Ultrasonic welding is a reliable method for manufacturing batteries.
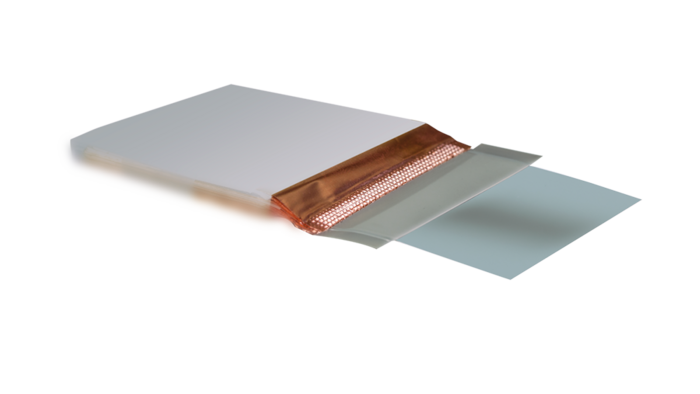
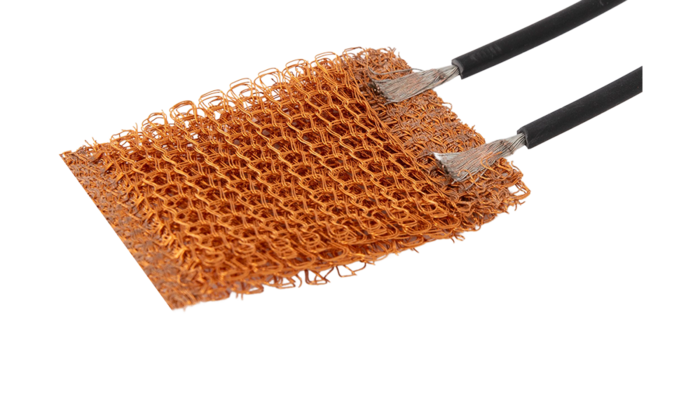
Automotive: In the automotive industry, manufacturers of cable harnesses rely on the ultrasonic welding technology. Components for car interiors are joined using ultrasonics. Components made of chrome, e.g. trim elements such as chromium rings, can be bonded.
Electronics: Cable and terminal connections can be welded quickly, safely and precisely using ultrasonic technology, with no danger to the sensitive technology.
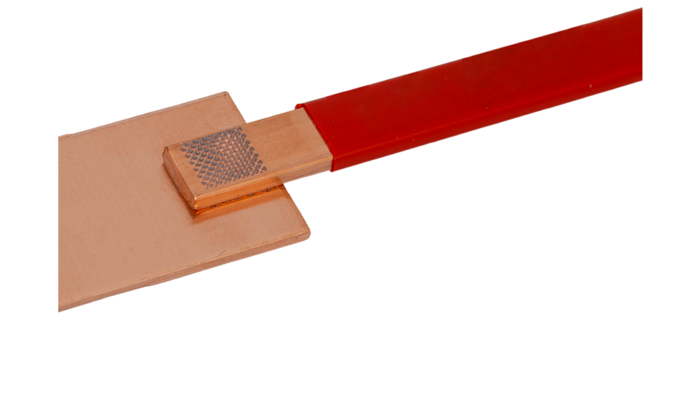